摘 要 广州地铁四号线直线电机车辆段基于整体道床的“零轨”铺设技术是目前国内外均未涉及的新技术领域,“零轨”铺设技术利用了支柱h型钢检查坑式整体道床,解决了轨道各项尺寸精度为1mm以内的难题,保证了直线电机机车车辆运行参数和直线电机气隙的精确稳定。结合工程实例,对“零轨”铺设的关键技术,即整体道床一次性整体成型技术、支柱式h型钢检查坑道床一次性成型技术进行了分析研究,对轨道尺寸精度调整所采取的一系列措施进行了总结。
关键词 直线电机轨道 整体道床 零轨铺设 精度控制
广州地铁四号线在国内首次应用了具有世界先进水平的中大运量直线电机运载系统,其直线电机车辆段是四号线的控制中心,也是四号线全线69.64km线路的车辆运用、调度、段内编组、车辆停放、维修、各种运营设备维修保养的重要场所。为满足直线电机车辆检修、直线电机的安装调试、直线电机本体与感应板之间气隙的测定调整等功能的综合需要,段内需在不同功能区不易变形的整体道床部位设置不同形式的高精度轨道———“零轨”。
1“零轨”的由来
与传统轮轨驱动系统不同,直线电机轨道运载系统的机车车辆采用与普通旋转电机不同的直线电机产生驱动力,它的电机由完全分离的两部分组成:板状的初级定子固定在机车车辆上,而次级转子演变为复合金属平板(即感应板)沿轨道线路延伸,并固定在道床上成为道床的一个不可分割的组成部分。定子绕组与转子之间的间隙———气隙的大小直接影响直线电机的驱动能力和工作效率。为保持直线电机车辆的良好状态,维持直线电机气隙的精确与恒定,除机车车辆各部件加工精度要求较高之外,工程上通常会采取很多保障措施。
(1)尽量减小道床加载后路基的工后沉降尤其是不均匀沉降,如加固碎石道床路段路基强度、强化压道整道措施、延长路基自然沉降期等;
(2)精确调整正线和车辆段内铺设感应板区域的轨道参数如轨距、高低、水平、轨向等,减小轨道系统本身偏差;
(3)通过提高感应板安装精度,确保感应板顶面与钢轨顶面的间距准确;
(4)在车辆段专用库房整体道床位置铺设高精度的轨道,并以此轨道作为机车安装调试基准轨,以减少机车车辆和直线电机本身的安装、调整、测量偏差。
以上第4种措施所述的高精度轨道以追求轨距、高度、水平、方向以及2条铁轨的平行度等参数误差趋近于零为目标,对于此种高精度轨道,国际上并无通用名称可参考,因而在广州地铁四号线车辆段工程中,该类型轨道被业主、设计、监理和施工各相关单位通称谓“零轨”。简言之,“零轨”就是为提高直线电机机车车辆的安装调试精度,精确调整检测直线电机定、转子之间的气隙而专门铺设的误差极小的专用轨道。
运营过程中,“零轨”主要在以下几种情况下发挥关键作用:一是新车上线运营前直线电机在机车车辆转向架上进行初始安装和调整;二是运营过程中直线电机气隙的在轨实时检测;三是在直线电机机车车辆状况变化时进行定检、定修、架修、大修理后的功能恢复;四是路基、轨道、感应板参数发生变化足以影响直线电机功效发挥时的气隙重新调校。
针对上述不同情况,广州地铁四号线车辆段段内分别在运用库的检查库内三条检查线、静调临修库的静调线和洗车机棚的洗车线分别铺设了8处共260m长的“零轨”段。
2“零轨”铺设的技术思路
1mm的尺寸精度对于机械加工行业来说比较容易实现。对于以钢筋混凝土浇注为主要工艺方法的整体道床轨道工程来说,实现难度就相当大。在广州地铁四号线车辆段轨道施工组织设计评审阶段,有关轨道工程专家对1mm的轨道标准要求提出质疑,并建议业主、设计修改“零轨”精度要求。但直线电机感应板的安装精度要求以及气隙调整的实际需要要求轨道尺寸必须满足这个标准。通过反复论证,最终确定,“零轨”技术的精确实现有赖于相互联系的两个工艺过程的准确达成:一是“零轨”的基础,即整体道床结构一次性整体灌筑成型,另一个是拟铺设“零轨”区段的轨道尺寸参数的精确调整。在广州地铁四号线车辆段的“零轨”铺设过程中,“零轨”的高精度分两个阶段通过渐次逼近的方法实现:整体道床结构施工完成后保证轨道尺寸精度在±2mm之内,然后通过反复调整使轨道尺寸最终达到0到1mm之间的“零轨”精度标准。
3“零轨”铺设技术
3.1 整体道床一次性整体成型技术
广州地铁四号线直线电机车辆段拟铺设“零轨”的整体道床有如下几种形式:一是普通长枕埋入式整体道床(见图1),轨枕中央的2个螺栓孔用于固定感应板,道床成型后,可通过增减感应板下方的调整垫片来调节感应板顶面距轨面的高度。二是库内横通道长枕埋入式整体道床(见图2),与普通长枕埋入式类似。道床成型后,先调整好高度并固定好感应板,最后将感应板与道床浇注成一个整体形成横通道。三是支柱h型钢检查坑式整体道床(见图3)。这种道床采用无轨枕支柱式设计,在钢轨与支柱之间首次应用h型钢过渡。h型钢的运用增大了轨道刚度,为“零轨”精度保持恒定不变提供支持,支柱间距也得以从原设计1.1m加大至2.2m,方便了检修作业人员出入检查坑。
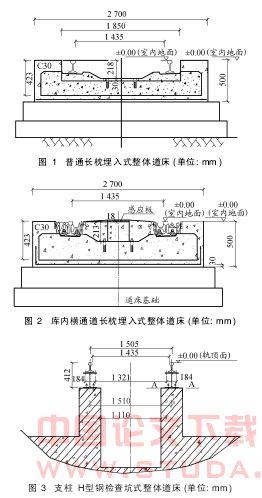
3.1.1 长枕埋入式整体道床成型技术
长枕埋入式整体道床一次性整体成型的要领是混凝土浇注成型后,轨道的的高低误差需控制在±1mm以内,只有如此才能满足感应板的安装要求,所以如何确保轨道的高低误差控制在±1mm之内,成为本长枕埋入式整体道床成型的技术难关和重点。图4为长枕埋入式整体道床成型工艺流程。
长枕埋入式整体道床一次成型的成败,取决于关键工序的工艺水平和施工质量。轨排组装、轨道各部几何尺寸调整、浇注支墩混凝土、浇注道床混凝土是道床成型的关键环节。
(1)轨排组装
轨排组装直接在整体道床铺设位置进行。其组装工艺过程是:
①按照设计要求的数量和间距,将锚固好的长轨枕散布于待铺设整体道床的线路基底上;
②散布扣件于长轨枕两端;
③在承轨槽内放置轨下胶垫;
④将配好的钢轨吊入承轨槽,轨腰上应标注短轨枕位置;
⑤按照设计的轨枕间距,调好轨枕位置,并上扣配件;
⑥安装轨距拉杆和摆放钢轨支撑架(2.5m布置一个);
⑦用自制门吊将轨排吊起,吊起高度(30cm左右)以满足钢轨支撑架的安置为宜;
⑧调整轨距拉杆和安装钢轨支撑架,使轨距基本满足1435mm要求,并拆下门吊,轨排由钢轨支撑架支撑。
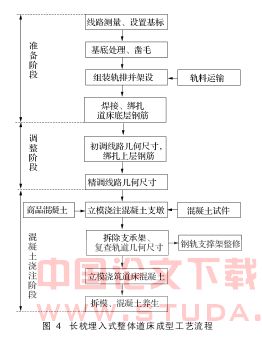
(2)轨道各部几何尺寸调整
由于整体道床必须一次成形、轨道各部几何尺寸精度要求高、且在混凝土浇筑前必须把轨道各部几何尺寸调至设计值,所以如何调整轨排至设计要求是整体道床成型中的重点和难点。通过对成型要求的分析理解,我们自行设计了一种适用于长枕埋入式整体道床一次浇注成型的上承式可调轨排支撑架。
轨排的调整定位程序是:先调水平→后调轨距→先调桩点→后调桩间;先调基准轨→后调另一轨→先粗调后精调的原则→反复调至符合标准为止。
①粗调定位。轨排经钢轨支撑架摆放就位后,以铺轨基标为基准,借助于直角道尺和万能道尺,通过钢轨支撑架丝杠对轨道几何状态进行初调。要求轨道目视顺直或圆顺,高程、轨距、水平及方向偏差均不超过±20mm(以减少精调的工作量),内外长轨枕对齐,上紧接头螺栓并保持轨缝对接。上承式可调轨排支撑架及轨排调整示意见图5。
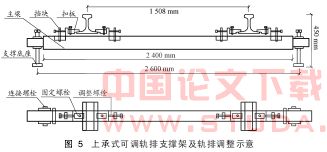
②精调定位。轨排初调完成后,采用弦线法、水准仪和万能道尺(精度允许偏差+0.5/0mm)等工具进行精调定位作业。具体调整中要注意以下几点。
a. 用直角道尺检查、调整其中一股钢轨。先将立柱高度调节至基标与轨面高差相适应,并将立柱底的对准器对准基标的中心孔,道尺滑动块架在钢轨上;
b.同时将万能道尺紧贴直角道尺架在左右两股钢轨上,检查两股钢轨的轨距;
c.调整基标前后相临钢轨支撑架,且先调水平再调中线;
d.旋转支撑架立柱,使钢轨升高或降低,直角道尺水准气泡居中时表示该股钢轨已调至所需高度,万能道尺水准气泡居中时,则表示另一侧钢轨也调至所需高度;
e.旋转支撑架上的轨卡螺丝(先松一侧再紧另一侧)使轨排左右移动,直至直角道尺水平滑块指针读数为0;
f.目测观察配合万能道尺和10m或20m长弦线丈量,旋转离基标较远的支撑架的立柱和轨卡螺栓,使钢轨平直圆顺;
g.在整个调轨作业中,由于钢轨支撑架的位置与线路基标不在同一断面上,钢轨与支撑架立柱又不在同一位置,以及某一支撑架调整时钢轨的刚性连动,调轨工作往往需要重复多次,反复调整,才能达到要求。
施工和检查用的直角道尺、万能道尺每天使用前必须在标准检测台作检查,如有误差及时调整。
(3)浇注支墩混凝土
调整好轨排各部几何尺寸至设计要求后,就每副轨排左右对称,每隔5根长轨枕选择连续2根,立模浇注支承墩混凝土。浇注时轨枕四周的混凝土要加强捣固,以确保轨枕底部支墩混凝土密实,支墩混凝土强度等级必须与道床一致(c30)。待支墩混凝土强度达到5mpa后拆除钢轨支承架和支墩模板。
(4)浇注道床混凝土
整体道床混凝土侧模采用建筑钢模。安装模板前要复查道床高程及轨道中心线位置是否符合设计要求,检查预埋件及预留孔洞是否遗漏,位置是否正确,确保模板安装正确。模板支立允许误差:位置±5mm,垂直2mm。
浇筑道床混凝土前,应再次检测轨道几何尺寸,确认符合验收标准后方可浇筑道床混凝土。道床混凝土采用商品混凝土,由混凝土运输车运输至浇注位置就位后,直接泵送入模。为确保施工连续性,混凝土浇筑应分层、水平、分台阶进行。混凝土的施工缝的接缝面与道床中心线垂直,施工缝设在伸缩缝处。使用插入式振捣器振捣并加强长轨枕底部及周围混凝土的捣固,道床表面需抹面整平,及时喷洒混凝土养护剂。
3.1.2 支柱式h型钢检查坑整体道床一次性成型技术
支柱式h型钢检查坑整体道床与长枕埋入式整体道床成型技术最大的不同就是在钢轨与混凝土道床之间设置h型钢。
(1)成型作业工前准备
①应根据设计图纸先预配好所需h型钢的长度和数量。
②计算每节h型钢所需的扣配件数量和安装位置,并预先在工厂对h型钢安装扣配件位置进行钻孔。
③由于支墩的间距为2.2m,所以钢轨支撑架布置间隔亦为2.2m。
(2)支柱h型钢检查坑式整体道床成型和调节工艺过程(图6)
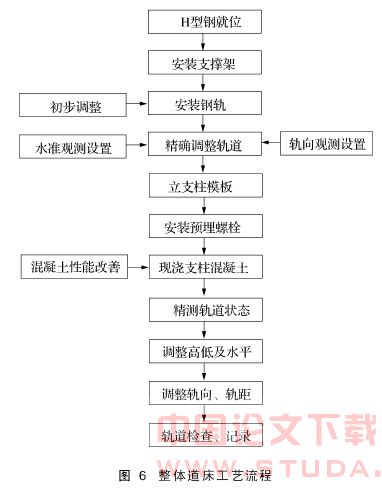
(3)成型过程中对技术要点的把握
①轨道铺设应遵循先用支撑架支撑h型钢,初步调整h型钢中线和高程,然后用扣板扣件联结钢轨和h型钢,初步调整轨面高低、水平、轨向、轨距。
②轨道调整应注意用直角道尺法测量轨面至控制基标的高差和水平距离,控制轨道高程和中线,用轨道尺长水准泡居中控制轨道水平,用弦线法检查并控制轨道轨向和高低,用轨道尺控制轨道轨距。轨道调整好后用横向支撑杆和轨撑进行稳定性加固。调整中本着先水平要素后方向要素的原则,采取反复调整消除彼此的相互影响,直至符合轨道铺设技术要求。
③在浇注混凝土时,注意降低施工荷载。
④采取这种支柱、h型钢、钢轨同时施工、一次成型的整体结构法成型技术,要注意加密支撑架,加密横向支撑杆,增加结构刚度,最大限度地消除各结构联结误差。
⑤改善混凝土性能:加入早强剂,提高混凝土早期强度,加入减水剂,拌制干硬性混凝土,减小混凝土凝固前自重力下沉;加入微膨胀剂,减少混凝土收缩。
⑥通过全站仪、精密水准仪的定位观测,在混凝土入模振捣后,立即找出施工误差,及时调整,再次振捣,以确保一次成型精度。同时控制每段“0”轨全长范围内整体道床轨道浇注成型后的精度水平、高低、轨向、轨距误差≤2mm。为下一步精调轨道参数做好准备。
支柱h型钢检查坑整体道床一次成型技术原理示意如图7所示。
3.2 轨道尺寸精确调整
通过一系列的控制措施,整体道床成型后轨道精度达到±2mm,加入调高垫板,先调整轨道高低和水平,再调整轨道轨向和轨距,最后细调局部精度,可使轨道精度从±2mm精确到0~1mm。
因为静调线有局部轮对精密检查装置使用的零轨段,实际调整过程中,我们的“零轨”全部按照0.2mm的调测标准进行掌握。用于“零轨”段精密调节的调高垫板是不锈钢板,厚度0.1、,0.2、0.5、1.2mm。因为垫板最薄为0.1mm,所以实现0.2mm的精度标准就有了物质和技术上的充分保障。
(1)调整轨道高低和水平。紧固扣件,精密水准仪设置在固定位置测量,在每扣件处标明与理论值的误差,松开扣件,在轨底加入调高垫板,紧固扣件,机车压道2遍,再测量一次,
重复上述步骤,反复调整高低和水平直至合格。
(2)调整轨道轨向和轨距。用全站仪穿线,逐个扣件处加入钢轨距块调整一股钢轨轨向,同时消灭钢轨与扣件的有害间隙,以此为基本轨用轨距尺控制轨距法调整下股钢轨轨向。进行逐点检查,反复调整局部细微误差直至合格。
(3)轨道质检。调整轨道轨向和轨距作业会影响轨道高低和水平,需经过调整-检查-再调整的重复工序。最终用设计规定的检查方法检查轨道,做好记录。使用中应定期进行检查,特别是在功能使用前,更应细致检查。
4“零轨”铺设误差的分析与改进(见表1)
5 需努力改进的方向
(1)轮轨的接触行车,产生对钢轨的向外挤压力,扣板式扣件压槽和轨底之间,扣件与螺栓之间的间隙影响轨道轨距和轨向,为保持“零轨”高精度的技术条件,需要重新考虑更换扣件类型。
(2)在运营过程中的在用状态下,轨下橡胶垫板受力后的压缩变形影响了轨道水平精度,建议更换橡胶垫板为非压缩性材料,以利于增加道床刚度,减小轨道变形,确保直线电机运载系统高效运作。
(3)站场路基处理应考虑锤击管桩等强化措施,稳定道床结构,减小路基变形,确保直线电机车辆平稳运营,确保直线电机气隙精准可靠。