摘要:荷兰鹿特丹dokhaven污水处理工程设计于20世纪70年代末,当时因地形限制而建于全封闭的地下,采用ab法,占地面积仅为传统工艺的1/4。运行伊始,氮、磷等排放标准便不断提高,处理工艺不得不逐渐升级。
关键词:ab法 除磷脱氮 尾气处理
荷兰鹿特丹dokhaven市政处理厂始建于1979年,负责处理来自鹿特丹市中心、南部与西部部分地区城市。其主体处理工艺构筑物完全置于地面附近存在大量居民住宅的地下,使之成为荷兰,乃至世界处理厂建设史上为数不多的经典工程之作。同时,因其与污泥处理工艺升级时不断采用世界上最先进的工艺流程,如 sharon(中温亚硝化)与anammox(氨氧化)等现代技术已生产化应用于其污泥消化液的脱氮处理之中,从而使它成为世界上技术装备最为先进的处理厂。它的总占地面积仅相当于普通处理厂的1/4,这意味着它不仅在能源与材料消耗方面有着很大程度上的可持续意义,而且在节省占地方面亦呈现出十分紧凑的可持续特点。此外,该处理厂在通风尾气的利用与处理、防振消音等方面的工程措施也有独到之处。
本文从dokhaven处理厂兴建的历史背景、工艺沿革、除磷脱氮、污泥处理、尾气处理、过程控制、安全防护等方面一一介绍该处理厂的情况,目的是使国内同行在跟踪先进处理工艺设计以及升级过程的同时,了解发达国家在处理设施建设方面的阶段性与总体发展思路以及具体工程实施办法。
1 历史背景
1977年荷兰zhew水务局决定在鹿特丹兴建3个市政处理厂,以处理从鹿特丹市排放的全部。其中一个打算建在鹿特丹市中心的处理厂选址在当时成了一大难题。在市中心vaanplein附近建处理厂不仅耗资巨大,而且也存在着很多棘手的问题,例如通向新马斯河的截流下水道不得不改变方向而穿过鹿特丹市中心地区。这些实际问题迫使市政当局寻找另外较为合适的场址,最后选定了dokhaven——一个已有一个世纪历史但已被废弃多年的船坞码头。
由于地表可用面积的限制以及周围已经存在大量居民住宅,处理构筑物不得不选择全地下式结构,而且能够利用的最大地下占地面积也仅为传统工艺所需面积的1/4。dokhaven处理厂于1979年决定兴建,1981年开始施工,1987年11月3日正式开始运行。
因占地所限,在处理工艺的现场不可能再兴建污泥处理与处置设施,只好将污泥送往距 dokhaven主场地 600 m以外的另一场地进行单独处理。同时,利用这一场地对从地下式全封闭处理工艺中排出的尾气进行必要的处理并排放。实际上,从dokhaven处理厂投入运行伊始,排放标准便不断提高。这意味着处理工艺必须顺应时代的要求不断升级与变型。在此方面,dokhaven处理厂不仅设计时便采用了当时最先进的ab法,而且在近两年内又及时吸收了研发于荷兰的最新脱氮技术——sharon与anammox工艺,最大限度地以较可持续的方式降低出水中氮的排放浓度。
2 排放标准提高与处理工艺升级
根据欧洲委员会《地面水污染协定》(75/440/eec及79/869/eec)与《市政处理协定》(91/271/eec)[1],荷兰为满足境内《地面水污染协定》的目标,相应制订了自己严格的排放标准——《市政排放规范》。处理厂出水不仅要满足这个规范对出水水质的要求,而且还不得不满足对臭味与噪音控制的需要,即满足《环境管理协定》所规定的内容。
原始工艺设计(1980年)并未考虑对氮、磷的去除(见表1),而新的《市政排放规范》明确规定从1995年起对磷的排放限制,而且从那时起对氮的限制也逐渐由对tkn 的控制转向对总氮的控制。显然,原始的设计不能满足对营养物去除的要求,需要进行升级。对于除磷而言,因场地的限制而不得不在原始的生物处理过程主流线上补充化学除磷步骤。而对脱氮来说,及时对污泥消化液采用了近年在荷兰研发出来的sharon和 anammox工艺。污泥消化液仅占全场进水总量的1%,而所含氮的负荷却占了总进水氮负荷的1 5%。因此,对这小部分水量进行集中脱氮处理可显著地降低总的出水氮排放浓度。
3 处理厂概况
表1 逐渐提高的排放标准与目前处理结果
指 标
分 阶 段 排 放 标 准
处理结果
1980年设计值
1995年起
2006年后
目前出水水质
bod(mg/l)
20
20
20
4
tkn(mg/l)
20
20
-
7.7
tn(mg/l)
- *
-
20
24
tp(mg/l)
-
1
1
0.8
ss(mg/l)
30
30
30
2 注:*表示未作要求。
处理厂处理构筑物全部设计于地下。首先,从原船坞地面向海平面以下 7~8 m要挖去厚厚的淤泥层,紧接着向下是3~4 m厚的砂层。原船坞码头便建在砂层以下的隔水(新马斯河)层上,因此,处理工艺流程也只能建在这个隔水层上。处理工艺施工采用干式法。处理构筑物现场原为码头,而现今已变成一个拥有5 hm2面积的公园。
全地下处理工艺构筑物占据两层,总平面面积为4 hm2。它的处理能力为47万人口当量,其中大约30% 来自于服务区域内商业。处理厂进水依靠5个终端泵站通过压力管道导入。原设计中的污泥消化液也通过压力输送回到处理厂(现已单独处理)。暴雨季节,处理厂最大小时处理能力为1.9万m3。
处理工艺为二级,首先去除悬浮物,然后为二段生物处理工艺(ab法)。最后,处理水用泵抽入地上的新马斯河排放。处理厂的主要投资用于防护性措施,以保证周围居民免于臭味、振动或噪音的干扰。
处理过程中产生的污泥用泵送往600 m以外的另一处约1 hm2的地上场地单独处理。污泥首先浓缩,然后消化。消化过程产生的甲烷用于发电,供应处理厂用电。每年从污泥消化产品——甲烷中产生的电量相当于2 750个荷兰家庭的用电量。最后,消化后的脱水污泥被运往鹿特丹以南的一个专用焚烧场做最终焚烧处置。
消化上清液(消化液)原设计为回流到处理工艺流程再行处理。但因2006年后对氮的控制将完全改用总氮标准,所以原设计显然不能满足要求 (见表1),必须寻求新的方法进行升级。由于原污 水处理工艺场地根本无余地再行扩建,所以dokhaven处理厂经过长时间的技术比较,最终选定了以sharon+anammox 处理消化液中高浓度氨氮的方案。
4 处理工艺
4.1 工艺流程
dokhaven处理工艺流程见图1。进水靠场外5个终端泵站以及污泥消化液回流泵通过压力管线被泵入进水池(1)。每条压力管线在处理厂内均可控制开启;发生故障时进水也可通过跨越管线而直接排入新马斯河。进水首先进入细格栅(2)。有4组用于去除漂浮物与纤维物质的细格栅,每组细格栅包括2个孔径为5 mm的转鼓,水流垂直进入,截留杂物靠水力挤压后收集。
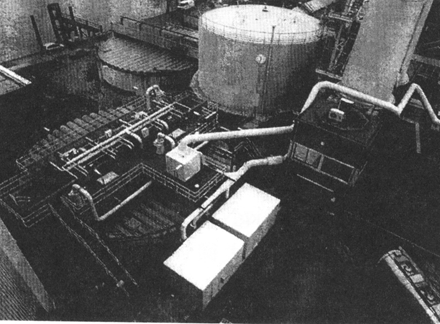
1 进水 2 细格栅 3 沉砂池 4 a段曝气池 5 中间沉淀池
6 回流污泥 7 剩余污泥回流 8 浮滓去除 9 污泥调节池
10 b段曝气池 11 最终沉淀池 12 出水排放新马斯河
13 剩余污泥至另一处理厂 14 格栅截留物排除 15 沉砂排除
图1 dokhaven处理工艺流程
通过格栅后,进水及此前回流的部分污泥经过一个配水槽被平行分为8股,各自进入一个完全相同的曝气沉砂池(3)。沉淀砂粒通过底部刮砂机排出并被冲洗后运出。
然后,进水以及部分回流污泥进入8个平行的a段曝气池(4)。因雨季时同雨水混合,所以雨季时的曝气池停留时间最短,为15 min;旱季时的正常停留时间为30 min。在a段曝气池中,cod 去除率约 80%,同时氮和磷也会因细菌合成或化学沉淀而显著减少。在a段曝气池中,铁盐、混凝剂与絮凝剂配合细菌代谢使用,主要作用是化学除磷。如果曝气池表面出现泡沫现象,还要投加除泡剂。
8个平流式中间沉淀池(5)负责对来自a段曝气池(浸没式微孔曝气)的混合液沉淀分离。底部刮泥机以及水面浮滓撇除板清除沉淀污泥与浮滓。回流污泥(6)靠16台大功率水泵回流至格栅前(旱季时),而在雨季时污泥直接回流进入a段曝气池。不断产生的剩余污泥(7)和被撇除的浮滓(8)通过一个调节池送往污泥处理部分。
由中间沉淀池分离的上清液(中间出水)依次进入4组b段曝气池(每组中设4个表面曝气器)。自动控制阀门让 b段曝气池保持一个恒定的水位,以确保稳定的运行。对b段曝气池来说,存在着一个最大的允许接纳水量。如果中间出水流量超过14 500 m3/h,多余的水量将被直接排入新马斯河,这种情况显然只在雨季时才会出现。b段曝气池再去除85%的有机物,加上a段曝气池较早已去除的约80%,两段曝气总有机物去除率为96% 。在b段曝气池中,氨氮通过硝化作用被氧化为硝酸氮。污泥在最终沉淀池(11)中沉淀分离,回流污泥(6)返回b段曝气池;剩余污泥(7)和浮渣(8)通过一个调节池送往污泥处理部分;最终出水靠出水泵排入有着较高水位的新马斯河。
整个处理工艺流程的水力停留时间为12 h,而传统工艺的停留时间往往需要48 h(如在荷兰广泛采用的氧化沟系统)。
4.2 工艺参数
设计负荷47万人口当量,9100 m3/h(旱季),19000 m3/h(雨季),14250 m3/h (最大b段进水量)。
格栅4组,流量为7200 m3/h,转鼓直径为1000 mm,孔径为5 mm。
曝气沉砂池8组,尺寸14 m×3.5 m×4.33 m (l×w×h),停留时间为5.4 min,粗泡曝气,总曝气能力为925~3 850 m3/h,吸砂泵为4台,流量为30 m3/h,2个18 m3沉砂贮存罐。
a段曝气池8组,尺寸39.6 m×3.5 m×4.32 m (l×w×h),停留时间为15 min,污泥负荷为3 kg bod/(kgmlss·d),细泡曝气,总曝气能力为4900~21800 m3/h,混合液浓度为1.5~2 kg mlss/m3。
中间沉淀池8组,尺寸60.5 m×13.1 m×2.6 m (l×w×h),停留时间为50 min,表面负荷为3 m3/(m2·h),链式刮泥机为16套,污泥回流泵为16台,流量为190~630 m3 /h,a段剩余污泥调节池为38 m3。
b段曝气池4组,尺寸27.2 m×27.2 m×4 m (l×w×h),停留时间为50 min,污泥负荷为0.15 kgbod/(kgmlss·d),表面曝气机16台,混合液浓度为3 kgmlss/m3。
最终沉淀池8组,尺寸83.1 m×17.2 m×2.5 m (l×w×h),停留时间为120 min,最大容许流量为14250 m3/h,表面负荷为1.25 m3/(m2·h),链式刮泥机16套,污泥回流泵流量为310~710 m3/h,b段剩余污泥调节池为35 m3。
出水泵站水泵为6台,每台流量为3400 m3/h。
5 自动控制
大量计算机被用于控制水泵的开启、在线水质/控制参数测量与仪表控制。计算机实际上负责着dokhaven处理厂大部分日常运行与监测工作,它们协调着与污泥处理工艺,控制着水泵站,保持着与鹿特丹市负责管理排水系统的中心通讯与控制室的联系。
原则上,dokhaven处理厂的与污泥处理部分均不需要人工操作。因此,全场包括工人在内的管理人员编制仅为27名,并实行正常的周末与假日休假制度,无轮班工作的必要。处理厂遇故障或事故时完全能以失灵后安全运行模式工作。同时,监视服务系统自动通过计算机报警。中心控制单元为分散式,总控制系统被分成8个子系统。这些子系统全装备有大量的可编程逻辑控制器(plc)。一旦总控制系统瘫痪,每一个子系统仍可独立工作。
控制室长期备用一套操作系统。一套运行系统失灵时,仍能正常工作。控制室也存储着历史数据和数据通讯库;数据通讯库将处理、污泥处理以及排水系统终端泵站三者间相互联系起来。
自1987年dokhaven投入运行以来,随着信息技术的发展它的自动控制系统不断得到更新和优化。新自控系统已于1999年开始使用,控制理念已现代化,从而保证着满意的出水水质,并使之不断得到改进。
目前,处理过程中的各种控制参数(如ph、溶解氧、氧化还原电位等)以及各种污染物浓度(如cod、氨氮、磷酸盐、硝酸氮等)已全部实现在线监测与控制。
6 污泥处理工艺
6.1 工艺流程
有机污泥作为一种能源载体,首先考虑将其中的有机物转化为含能气体——甲烷。以此为核心,形成如图2所示的污泥处理工艺。来自于处理过程产生的剩余污泥在进入污泥消化池(5)前存在两种不同的浓缩方法。来自于a段曝气池的剩余污泥和浮滓在浓缩前先经过一个细格栅(1)过滤,然后平行进入两个重力浓缩池(2)。沉淀污泥含水率为94%;分离出的上清液再回到处理工艺进一步处理。
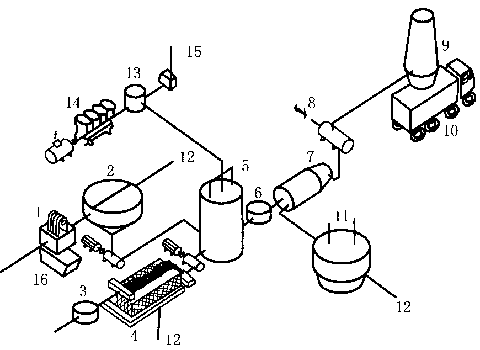
1 细格栅 2 重力浓缩池 3 调节池 4 带式浓缩机 5 消化池
6 调节池?7 离心机 8 污泥泵 9 贮泥罐 10 运至污泥焚烧厂
11 sharon反应器 12 至anammox反应塔 13 贮气罐
14 燃气发电机 15 高空燃烧烟囱 16 被去除固体处置
图2 污泥处理工艺流程
来自于b段曝气池的剩余污泥和浮渣则进入不同的线路。首先,进入一个带搅拌器的调节池,以求得到完全混合均匀。然后,污泥进入一带式浓缩机,使污泥含水率降至94%。浓缩过程使用絮凝剂,以利于污泥脱水分离。被脱除的水分同样再回到处理工艺进一步处理。
经两种不同浓缩方式浓缩后的污泥一同进入两个相同的消化池。消化池温度保持在33 ℃,停留时间约为30 d。为了保持消化池内污泥的良好混合,800 m3/h消化气由射流管打入消化池。消化气被贮存在贮气罐(13)中,由热电厂(14)发电和供热。自发电力被用于本场与污泥处理过程电力供应。热电厂也具有应急发电厂的功能。当由消化气产生的电力不足时,发电厂补充天然气进行发电。若消化气过剩,多余的气体则被燃烧后通过大烟囱(15)排放。热电厂产生的余热用于加热消化污泥和冬季办公室取暖等场合。
消化后的熟污泥进入调节池(6),并在此投加絮凝剂以利于最终脱水。最终脱水靠两台离心机完成,每台离心机的处理能力为40 m3/h。离心脱水后的污泥含水率为70%,被贮存于两个贮泥罐(9)中,等待运出场外焚烧处置。原设计中污泥消化液被回流至处理工艺进一步处理。
污泥消化液含有相当高的氨氮浓度(最高可达1500 mg n/l),水温为28 ℃。如此高的氮负荷进入处理工艺会加重氮的去除负担。正因为如此,采用最新的sharon与anammox技术对污泥消化液实施单独脱氮处理是近年来dokhaven处理厂升级的最新措施。世界上第一座生产性sharon反应器(11)已于1998年10月开始在此运行,世界上第一座anammox反应塔(12)也在2002年6月投入运行。
6.2 工艺参数
细格栅1组,流量为510 m3/h,栅间距为3 mm。
重力浓缩池2组,ф23.6 m,h=3 m,干固体负荷为36 kg/(m2·d),污泥体积为530 m3/d(含水率94%)。
带式浓缩机处理能力为90 m3/h或700 kg干固体/h。
剩余污泥调节池为900 m3。
污泥消化池2组,ф22 m,h=23 m,停留时间为33 ℃时28天,消化后污泥体积为600 m3/d(含水率96%),熟污泥调节池为900 m3。
离心机2套,处理量为40 m3/h。
脱水熟污泥贮存罐2个,体积为150 m3;停放时间为2.5 d;h=14 m。
sharon反应器1组;ф19.5 m,h=5.75 m,流量为550 m 3/d,水力停留时间为3 d,好氧停留时间为24 h,温度为35 ℃,ph为7~7.2,溶解氧浓度为1.5 mg/l。
anammox反应器1组;ф2.2 m,h=18 m(v=70 m3),流量为550 m3/d,水力停留时间为3 h,设计负荷为800 kgn/d,温度为35 ℃,ph为 7.5。
7 除磷脱氮
dokhaven处理厂在它1987年投入运行后已升级多次。除经济利益的驱动外,主要是因为环境标准的不断提高。出水对磷的限制早在1995年便已非常严格,要求出水磷的浓度最高标准为1 mgp/l。这意味着原始设计不能满足排放要求,处理工艺必须升级。因受场地限制,一种精心设计的化学方法被选择在 a段曝气池进行除磷,这是因为若在b段曝气池实施化学除磷会影响硝化过程。一种铁盐、一种混凝剂、一种絮凝剂被结合在一起用于化学除磷,这种方法称为“三药剂”方法。这种特殊的方法比传统化学方法能节省40%的运行费用。因此,可做到环境与经济效益上的双赢。[kg)]
从2006年起对出水氮的限制将由现在的tkn改为总氮控制。显然,原始设计不能满足新的要求,不得不寻求适合该处理厂特点的新方法。sharon和anammox这两项最新的现代技术因此成了单独处理污泥消化液的首选。根据sharon技术原理,带余温的污泥硝化液刚好满足中温亚硝化对温度的需要。sharon技术除节省 1/4供氧量的特点外,还具有低的投资费用、低的运行费用、不产生化学副产品、运行维护简单、启动容易、对高进水ss浓度不敏感、无异味等运行优势。图3为一sharon工艺的现场图片。
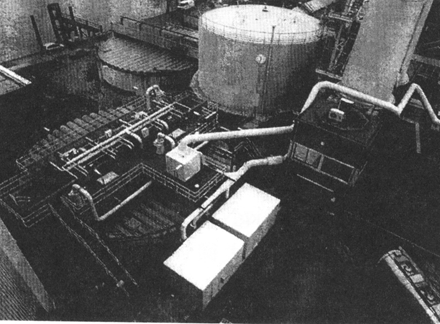
图3 sharon工艺实际构筑物
sharon反应器使一半的氨氮氧化至亚硝酸氮(无需控制ph),剩余一半氨氮与转化而来的亚硝酸氮(进水总氨氮的一半)刚好形成1∶1 anammox所需的摩尔关系,使氨氮和亚硝酸氮自养直接转化为氮气。与传统的硝化/反硝化过程相比,sharon/anammox过程可使运行费用减少90%,co2排放量减少88%,不产生n2o 有害气体,无需有机物,不产生剩余污泥,节省占地50%,具有显著的可持续性与经济效益特点。图4显示了气体循环anammox反应塔现场实物图片(利用一废弃浓缩池改建而成)。经sharon/anammox对污泥消化液单独进行脱氮处理可使整个处理厂出水氮浓度下降至少5 mgn/l,与原始设计相比出水刚好能满足未来出水标准。

图4 anammox反应塔现场实物
8 通风、尾气利用与处理
因为dokhaven处理厂处理工艺部分置于全地下,所以通风以及被污染的空气(尾气)处理便成为处理厂中工程上必须要妥善解决的问题,以保证良好的工作环境和工艺过程有充足的空气供应,同时尾气排放又不致污染大气。
好的工作环境包括防止凝结水出现,避免有毒、有害气体散发,通风便显得十分重要。全地下设置的处理构筑物不可能实现自然通风,所以dokhaven处理厂便选择了压差通风系统:处理工艺区内压力低于各工艺区间连接走廊压力。因此,即使工艺区通往连接走廊的门是开着的,工艺区被污染的空气也不会进入走廊。在走廊系统中,共需66 000 m3外部空气和34 000 m3循环空气。所有这些空气中,由于压差每小时会损失4 600 m3。走廊系统中的空气也用于一些工艺区的通风,如最终沉淀区、化学药剂区、沉砂冲洗区等。
在中间与最终沉淀区的空气受到轻微污染,而这些区域是工作人员经常出现的地方。按规定,这些区域的h2s含量不得超过0.1 mg/m3,所以中间沉淀池也需要用外部空气通风。中间沉淀区被外部通风交换出的尾气被用于a段曝气池与曝气沉砂池曝气,在曝气供氧的同时将h2s等有害气体实现生物转化。一些重污染工艺区的空气也使用来自于中间沉淀区受轻微污染的尾气通风。走廊系统中的空气被用于最终沉淀区通风,其尾气大部分被用于b段曝气池曝气,一小部分也用于a段曝气池曝气,同样具有供氧与转化有害气体的双重作用。从中间与最终沉淀区被交换出的多余尾气通过地下管道被送往污泥处理区,经60 m高架烟囱排放排入大气。
重污染空气出现在被封闭的工艺区,此处h2s含量很高,不允许工作人员无保护措施进入。这些被封闭的工艺区通风靠来自于轻污染区尾气进行。办公与服务楼、车间、变压器室以及高、低压区域用外部空气通风。这部分尾气因未受到污染,可直接排入大气。显然,来自重污染工艺区的尾气不能被直接通风排出,应该被妥善进行尾气处理。对此,dokhaven处理厂采用了湿式化学气体洗涤系统。该系统由三个平行的通道组成,其中一条留作备用。每一通道的处理能力为45 000 m3/h。每组通道均由三级组成。在前两级,重污染尾气用次氯酸钠漂白剂与氢氧化钠溶液洗涤。次氯酸钠可氧化硫化物到硫酸盐,使h2s不再出现。在第三级,仅仅使用氢氧化钠溶液,以去除残余的氯化物和微量有味气体化合物。脱矿化物水被用作清洗水,以避免尾气清洗系统受石灰或碳酸钙的侵蚀。
污泥处理区的空气也可能受到污染。可能出现污染的工艺区全被加盖、封闭,并采用机械通风。被污染的尾气通过2个四级化学洗涤装置处理。在前三级中,被污染的尾气用次氯酸钠漂白剂与氢氧化钠溶液洗涤。在第四级中,仅仅采用氢氧化钠溶液洗涤。
9 运行安全性
能够将一些危险物质带入处理厂,所以现场必须有足够的防范措施,以保障厂内工作人员以及附近居民的安全。另外,还应设置有效的防振与消音设施。
倘若附近地区有爆炸物发生爆炸(此种情形在荷兰曾发生过),爆炸物就会通过下水道流入处理厂。为避免此类事故发生,处理厂已采取了下列一些具体的安全防范措施:
(1)所有工艺过程以及可能接触可燃气体混合物的其它地方必须严格按照安全标准建造。
(2)所有终端泵站以及处理厂各个环节要配备易燃、易爆气体检测系统。一旦检测到这些气体的存在,控制系统便会自动将运行工艺转向事故安全运行模式。
(3)终端泵站的液位仪应予以格外保护。
(4)设有一容积为35 m3的可燃物临时贮存空间。
(5)热电厂设有应急发电设备。
距离处理厂最近4 m便存在居民住宅。显然,当地居民不愿受到任何讨厌、烦心的干扰。然而,处理厂众多的机器、水泵恰恰会产生巨大的振动和大量的噪音,特别是那些通风系统与分流设备。为了最大限度地减少可能产生的任何干扰,整个处理厂被分割成若干小的部分,并以泥浆与玻璃做成分隔墙。为了防止振动影响附近居民,水泵和其它设备全被安装在弹性混凝土底座上。进一步的抗噪音措施是在生产区与上部的服务区间设置110 cm厚的地板,以阻隔所有振动和噪音。
10 运行处理效果(见表2)
表2 dokhaven处理厂1999年上半年处理结果
项 目
a段
b段
总计
bod去除率(%)
76
85
96
tkn去除率(%)
24
81
86
tn去除率(%)
24
17
37
tp去除率(%)
68
41
81 注:
(1)接纳负荷47万人口当量,流量121000 m3/d。
(2)a段污泥浓度2000 mgmlss/l,污泥负荷3 gbod/(gss·d),svi 66 ml/g;
b段污泥浓度3100 mgmlss/l,污泥负荷0.13 gbod/(gss·d),svi 106 ml/g。
(3)污泥产量(消化后)16.7 tds/d,产生电量550万kw·h/a。
参考文献
1 ec.eu focus on clean water.isbn 9282848361,belgium, 1999
2 zhew.dokhaven on reflection.p o box 469, 3300 al dordrecht, the netherlands, 2000